Ceramic Cores
Our Ceramic Cores have been used in the creation of complex forms for very demanding pieces investment casting. With distinguished advantages such as high geometric accuracy and smooth casting surface, it is suitable for the formation of complex thin-walled parts. Ceramic cores contribute to improve the product performance, reducing structural weight and also manufacturing costs.
Our ceramic cores have excellent dimensional accuracy and shape stability at very high temperatures, which helps to improve highly casting accuracy.
- Adjustable shrinkage(0-1.8%) and strengths according requirement
- Tolerance precision <0.03mm
- local wall thickness can reach 0.3mm
- Excellent surface smoothness can reach 1.6 – 12.5 μm
- Weight of casting ranges from a few grams to tens of kilograms
- X-Ray capability to confirm and or detect internal/external defect gaps
- Each ceramic core is rigorously tested by internal and external trials
Different series of ceramic cores can be applied to the casting of high temperature alloy, titanium alloy, stainless steel alloy and aluminum alloy.
Applicable casting methods: DS, Equiaxial, Single crystal, etc.
Technical characteristics
Material Composition | Value | Note |
SiO2 | 90-95% | |
Al2O3 | 1-10% | |
Other | 1-8% | |
Typical Properties | Value | Note |
Shrinkage (mold to fired) | 0,50% | Can be tailoered to achieve specific shrinkage. |
Modulus of Rupture (MOR) | 30MPa 15MPa | Impregnated @RT @1500℃ |
Apparent Porosity | 30% | |
Thermal Expansion | 0,20% | RT to 1550℃ |
Leachablity | 100% | Autocalve NaOH |
Ceramic Cores for Super Alloy
Application:
- Equiaxed , DS, and single crystal casting
Advantages:
- High-temperature endurance
- Appropriate product strength
- High dimensional stability
- Leached type: Autoclave NaOH
Ceramic Cores for Stainless Steel
Advantages:
- Max service temperature: 1700℃
- Excellent chemical resistance
- Inactivity against metals during casting
- Easy to remove: Low residual strength
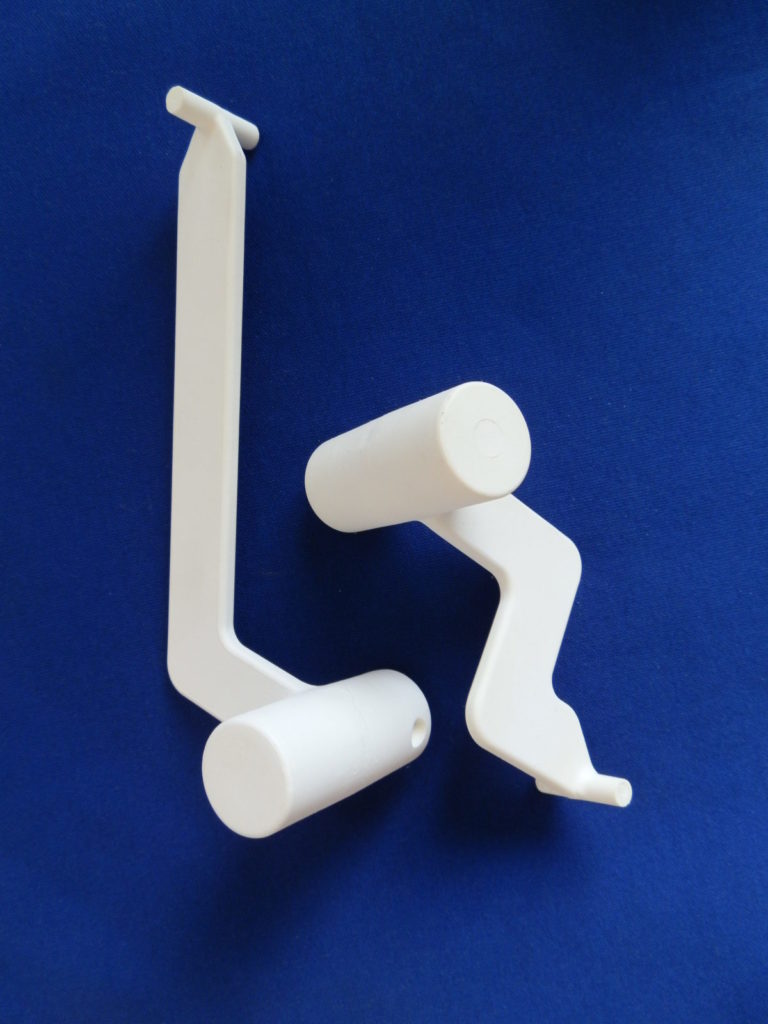
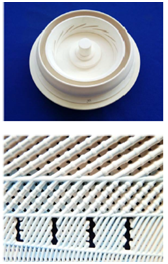
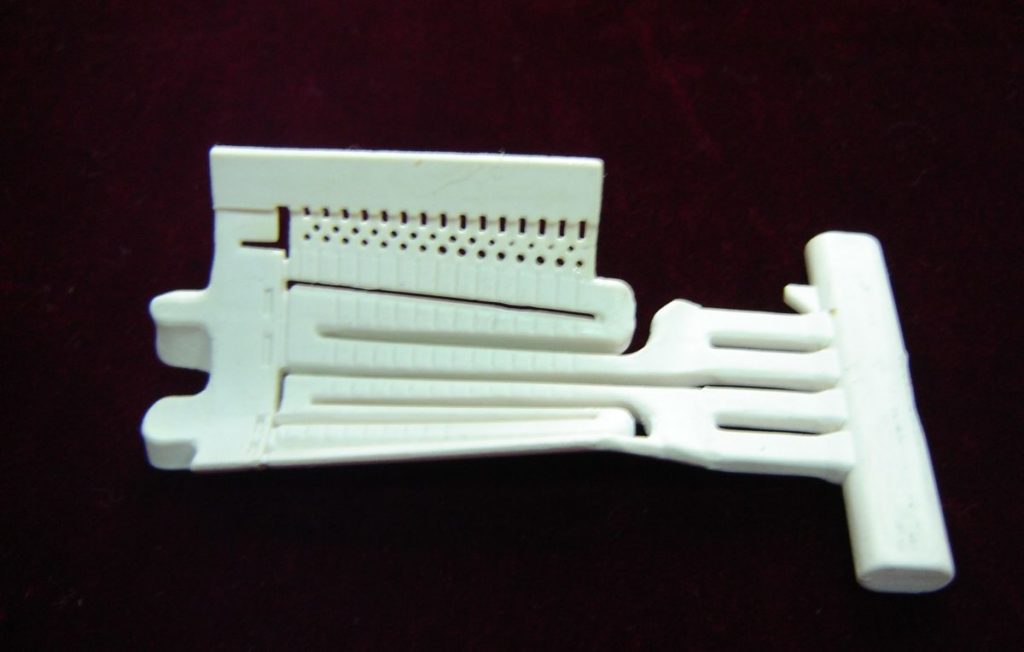
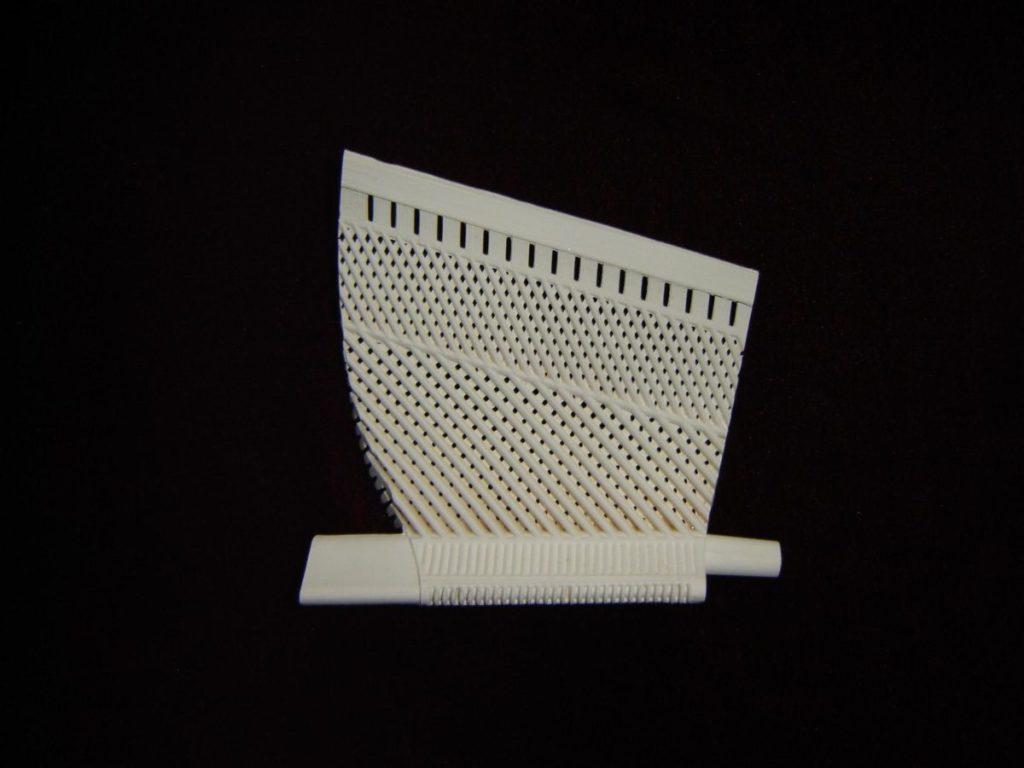
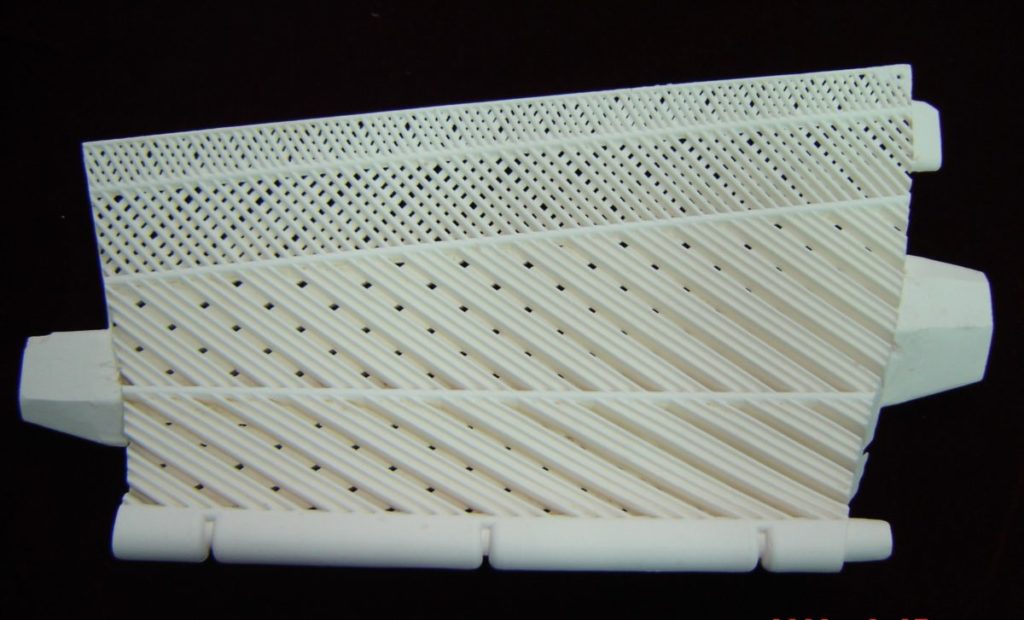